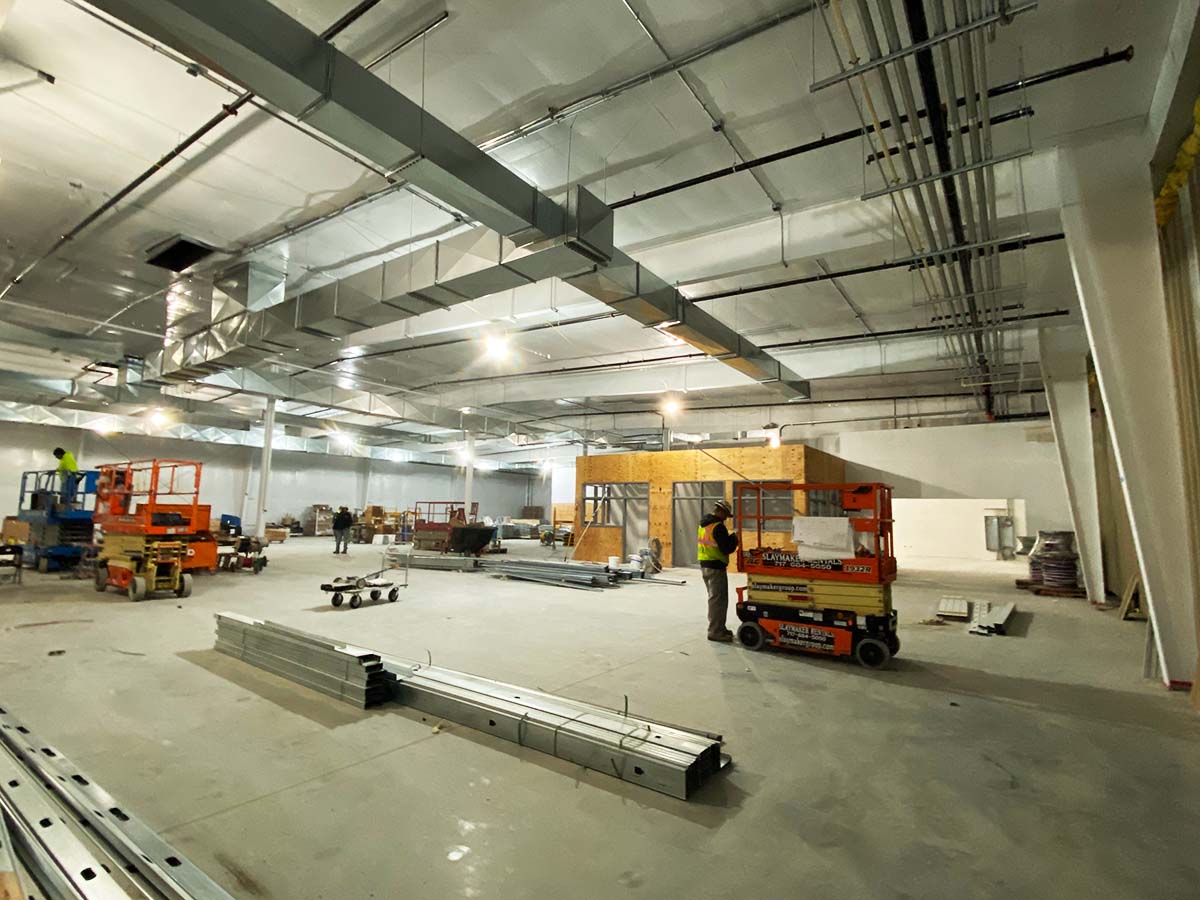
THE TRUE MEANING BEHIND YOUR CONSTRUCTION PROJECT DELAYS
With many industries returning to mostly normal operation following the COVID-19 pandemic, you may be wondering why you are still seeing delays in your residential and commercial construction projects. In short, these setbacks are due to supply and transportation disruption, material cost escalation, and workforce absence. Each of these factors impacts the others and increases the risk of a project becoming delayed. By working with TONO Group, our team is able to work with you to ensure the risk of project delays and the effects of cost escalation are mitigated.
SO, YOUR CONSTRUCTION PROJECT IS DELAYED? WHY IS THIS HAPPENING?
Supply Chain/Transportation Disruption
Delays within global supply chains and transportation were already present prior to the pandemic. Tariffs and sanctions implemented against several countries led to multiple sectors of industry stocking up on inventories to avoid the pending additional costs. The events of COVID-19 only made matters worse.
Throughout the first half of 2020, a majority of the nation (and our global community) went into lockdown which resulted in a reduction of manufacturing and construction efforts. Halfway through the year, there was a resurgence in the economy which led to an increased demand for building materials such as lumber and steel. On top of difficulty producing the materials in demand, there continues to be a struggle in getting products to their desired destinations.
These difficulties are caused by numerous factors such as increased shipping rates, congestion within ports, and labor shortages within the trucking industry.
Increased Shipping Rates
The cost of shipping goods has significantly increased in 2021. This is due to a lack of shipping containers which are essential for the transportation of goods. The limited availability of containers is caused by a low turnover rate. This further increases the demand which additionally raises the costs.
The most significant increase was seen between the US and China trade routes. It has become 13 times more expensive to have containers shipped from China to the US than it is to have them sent to China. This results in many carriers taking empty containers to China to meet the high demand.
Congestion Within Ports
Congestion within ports is an additional issue that is causing supply chain disruption. It has been noted that production is up significantly within ports to account for increased shipments, however many struggle to avoid delays. This is largely due to a labor shortage within the trucking industry which inhibits the ability to make space available for incoming shipments. Further delays have also been caused by isolated extreme weather events.
Trucking Industry Labor Shortage
The primary cause of supply chain discrepancies is a shortage of drivers. The pandemic has led to decreased numbers on the road which results in shipments sitting idle and creating a backlog from which it is difficult to recover.
A large portion of these drivers work for small firms which are also experiencing increased costs to operate their businesses. This results in lower margins which makes it difficult to stay in operation. The decrease in personnel has several contributing factors, but numerous companies are offering increased wages, sign-on bonuses, and unprecedented compensation.
Material Cost Escalation
In the early months of 2020, there was a significant decrease in the demand for nearly all construction materials. As the economy began to recover from the effects of the pandemic, there was an increase in the demand for common building materials such as lumber and steel which significantly raised material costs.
Lumber
Prior to the pandemic, Canadian and Pacific Northwest forests and mills were some of the primary sources of lumber in the United States. However, forest fires and a spreading mountain pine beetle infestation have destroyed usable forests which led to an increase in lumber prices. To counteract this, numerous lumber mills were built in the southern United States due to a surplus of lumber being available. The construction of these mills already has a long lead time, and the effects of the pandemic have further increased the lead times for some mills. While numerous mills are already in production, most face labor shortages due to either COVID-19 outbreaks or the inability to find workers.
In addition to existing issues, the pandemic added an even higher demand for lumber. With a significant number of homeowners working remotely and unable to travel, there was a sharp increase in do-it-yourself (DIY) and contracted home improvement projects. One of the largest impacts to lumber demand was from new home builds which drastically increased during this period due to extremely low mortgage rates.
Fortunately, the home improvement strain on the lumber market is subsiding and helping decrease prices, but it is anticipated that the determining factor for a stabilization and decrease in lumber costs will be determined by the duration of the low mortgage rates. As the demand for the lumber decreases, so will the cost.
Steel
In the beginning of the pandemic, many steel mills scaled back production in anticipation of a recession. Similar to the lumber market, steel also experienced a sharp increase in demand which overloaded mills. With additional income available and less to spend it on, consumers began to purchase new products which require steel. This resulted in the cost of steel reaching all-time high prices.
Unlike the lumber market, it is not anticipated that the price of steel will decrease soon. Although there has been a decrease in the purchase of steel-heavy products, many industries that require steel, such as manufacturing, oil, and gas, are seeing an exponential growth of demand. There is currently a limited supply of steel to fulfill these requirements, but as more steel is made available, it is anticipated that the costs will decrease.
Workforce Absence
Labor shortages were already an issue within the construction field. As with the other factors, this was only worsened by the pandemic. Many construction companies are having difficulty either retaining or attracting personnel. Several companies have gone to great lengths such as increasing base pay, offering sign-on bonuses, and providing benefits that are not typically available.
The largest hardship faced is finding the qualified personnel for the job. Many factors contribute to this shortage and efforts are in place to bolster the numbers, however this causes limitations in the amount of work that many companies can perform. This results in increased lead times for project completion and increased costs to account for increased wages and personnel training requirements.
MITIGATING DELAYS AND REDUCING UNNECESSARY COSTS
By employing our distinctive turnkey project delivery approach, TONO Group offers an integrated team of design and construction professionals. Through careful forethought and advanced planning, the architects and contractors at TONO collaborate in real time to develop creative building solutions while remaining mindful of industry trends.
With dozens of commercial projects, industrial projects, institutional projects, and residential projects, in various phases of development at any given time, team members within the construction unit provide invaluable feedback to the designers regarding materials shortcoming forecasts and market inflections. During the earliest stages of planning, our architectural team adjusts plans in real time to make critical decisions that may impact delivery months down the road.
The integrated team forecasts together to take advantage of anticipated trends and specifies building systems and material applications appropriate to the fluid market. This provides a unique advantage to our clients by alleviating stresses on the project pipeline. Moreover, the construction team provides critical early cost estimating efforts through the first stages of project planning including necessary expected materials and labor escalators to equip clients with informed budget forecasts.
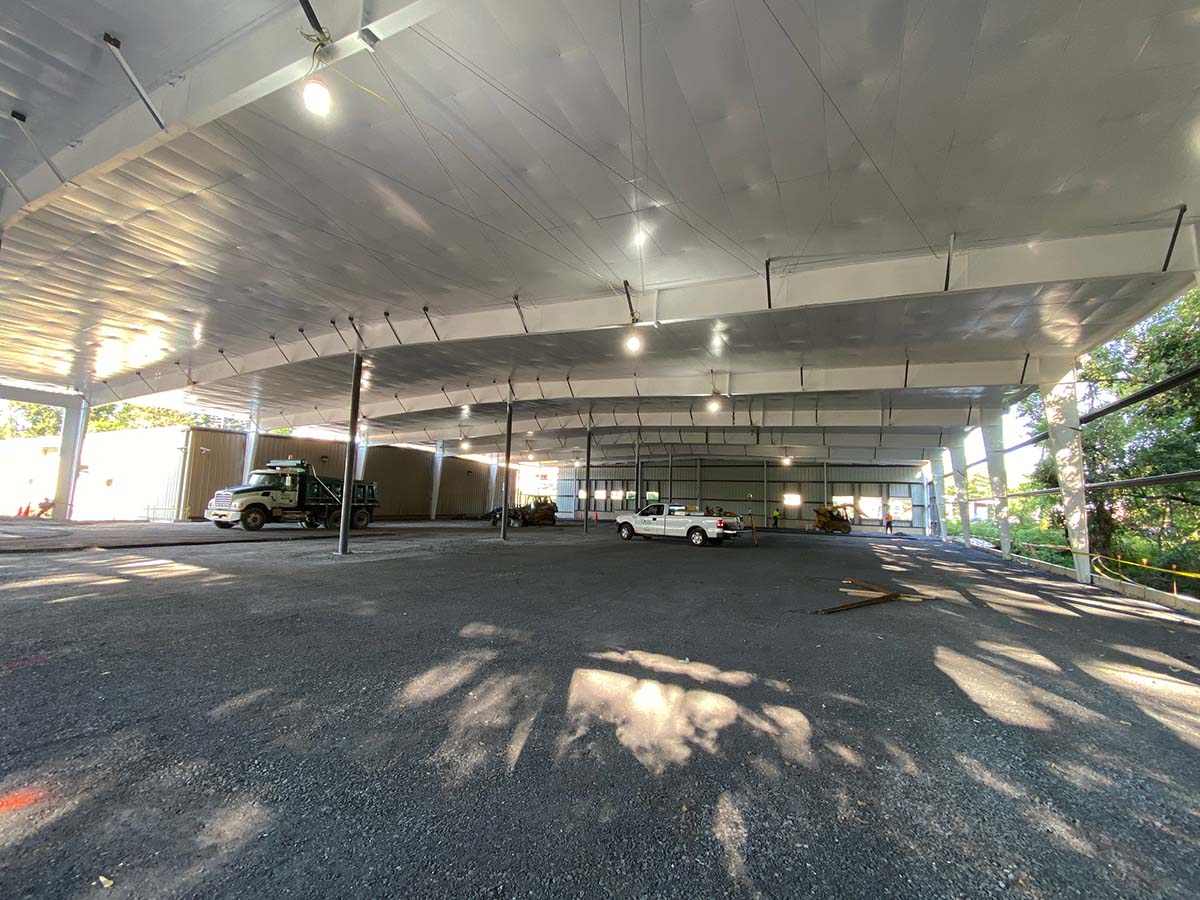
Flex Cell Precision- Commercial Construction Project
Early Planning
Decisive steps early in the planning process will yield dividends over the duration of any project. In the current supply chain crisis however, this strategy can be the difference between project success and failure.
By effectively anticipating the dynamics of the marketplace and providing our clients with key data to make informed decisions, our designers and construction experts are seen as invaluable team members in the continuum of project delivery.
For example, through initial planning on a manufacturing plant expansion in Lancaster County, Pennsylvania, the team recommended early engineering and purchase of the steel building components months in advance of construction start to ensure their timely delivery, but more so, to reduce the purchase price ahead of anticipated materials escalations. This strategy alone reduced the construction schedule by four months and provided significant direct financial benefit to the client.
Ability to Pivot
While early planning is paramount in the success of any project, remaining agile throughout its duration may be of more value during the post-pandemic era. As supply chains are broken or slowed, construction sequences may need to be altered to keep projects on pace.
Through frequent and effective communication with suppliers, subcontractors, and building inspection agencies, our team has successfully navigated this changing environment.
During the same industrial expansion project, our construction project management leadership elected to accelerate the installation of mechanical and electrical rough-in components when the interior partition framing material became inexplicably delayed days in advance of scheduled arrival. The team was able to provide scheduling incentives to specific trades to maintain project workflow without adversely impacting the end date or project cost.